Introduction
Cela Smith is the board chairperson at Ace Makerspace. Given the current state of rebuilding that Ace is going through, I thought it would be useful to learn from an executive what’s going on, while also finding out more about another member of Ace. I’m Carter Jenkins, and I had the opportunity to talk with Cela about what she does and how she does it.
History with Ace
Most board members at Ace end up in their position by volunteering their way up the ranks. They start as being regular members, then over time eventually make the shift to becoming a leader in the place they love. Cela’s story, however, was a bit different.
Cela found Ace through Board Match, a networking service that allows non-profit organizations to meet highly skilled professionals in the hopes of recruiting them to a board position. In one building, more than 100 non-profit organizations had gathered to recruit new members. Cela eventually found herself at the booth for Ace, something she had never heard of. However, she quickly learned that Ace was a place that could offer a lot to her. As someone who was interested in education, science/technology, animals, and nature-conservation type stuff, Ace offered a great window into science and education. This prompted Cela to take a tour of the physical space and after that, she was hooked. 2 years later, and Cela is still here doing what she loves.
Upcoming Things at Ace
Despite the recent COVID surge, the officers and the board have some big plans in the works. First, public events are coming back, like those hosted at the Oakland Public Library and Oakland First Fridays. The events, while being a good way to get the word out about Ace, are also incredibly fun for both the participants and the members arranging them so Cela is very excited to have those back. The other is the project-based learning system (I touched on this in another article, you can read about that here). Ace already classes on how to use tools and things like that, but with this new system, you’ll be actually building complicated things that you could take home with you and actually use/look at.
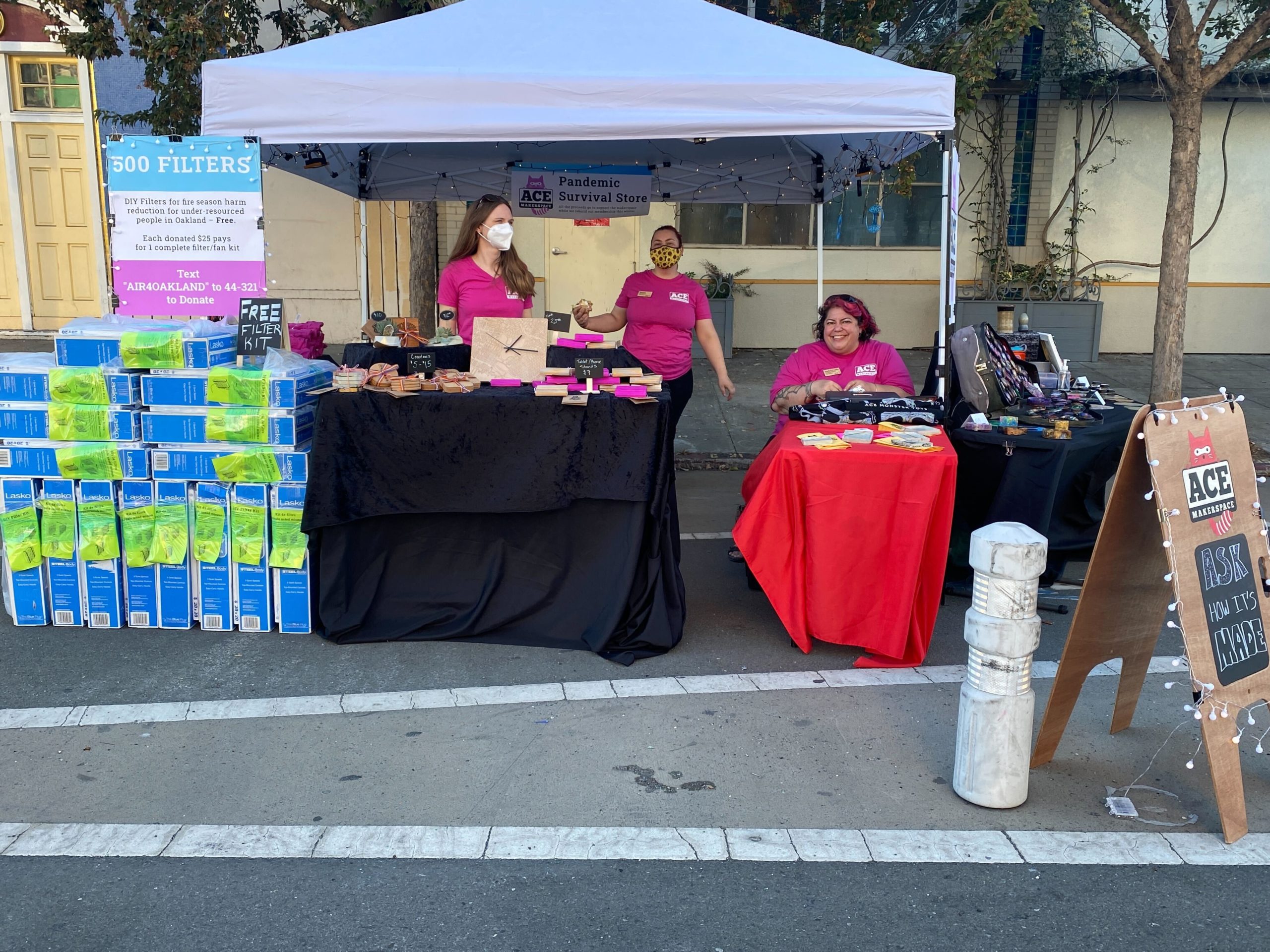
A Few Words from Cela
I asked Cela about what advice she would give to future board members, and what she said was so well thought out that I decided to put it right here, word for word.
“It’s important to be open-minded and flexible. When you’re trying to help out a non-profit, you want to help to guide things in a certain way. Of course, it’s never going to be 100% what you expect, you need to be ready to adapt to the needs of the organization instead of pushing your own agenda onto the org. Having respect for other people is also very important. It’s essential to remember we’re all just people, so even if there are differences of opinion we still need to respect each other.”
To wrap up, Cela loves being in the maker space itself. Walking around, she can get a lot of cool ideas for projects. Even if she doesn’t end up doing them, it’s great to see creativity in action. With a love of the spaces’ values and its ability to be for a broader community for more than just makers, Cela is grateful for the opportunity to be at Ace. I’m Carter Jenkins and thank you for reading.
Interested in joining the Ace Makerspace Board? Contact “board@acemakerspace.org”